Optimal service for full customer satisfaction
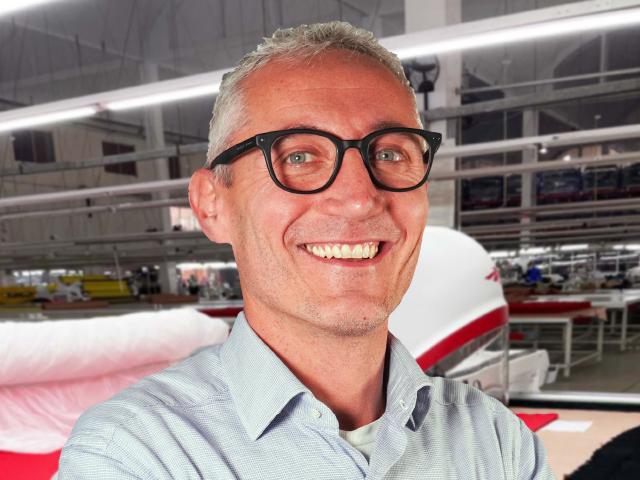
Nicola Donini / Director of operations
In terms of Operations, significant changes are taking place at Morgan Tecnica: streamlined production, following Lean Manufacturing principles; new supplying dynamics, with a focus on rationalizing the Supply Chain; and a completely revamped service. Nicola Donini, Director of Operations, shared this with us .
Nicola Donini commmented: «Our most important game is played when we finalize the installation and after-sales service». He manages all operational aspects at Morgan Tecnica: production, including planning and procurement, inbound & outbound logistics, operational quality, machine installation, and related service. This global perspective allows him to have full control over the entire company cycle.
THE RENEWAL OF THE SERVICE
«Our business card is the way we assist customers using our machines. That’s why we’re moving forward with a project that allows us to offer a completely revamped service».
Donini explained that from March 2024, began the renewal of the Service department, which was divided into two macro-areas, delineating the two separate worlds of Customer Care and Customer Service, followed and managed by two different managers. «We were guided by the beacon of total customer satisfaction. Therefore, we structured a more comprehensive service, including a series of targeted activities such as specific training for installers and customers».
This theme sheds light on the utmost importance, for those who use the machines, of having internal skills to perform maintenance or simple repairs in real-time.
SERVING CUSTOMERS
«In the area of Customer Care, we have also created the MorganTecnica Academy, a great innovation that provides not only an internal training school, but above all one outside the company. We have 5 branches, many distributors, and installers scattered all over the world. Our mission is to specialize them in every type of machine that characterizes Morgan Tecnica’s complete offering».
«We will continue to deal with what I call “the firefighting department”, that is, the Customer Service that intervenes in case of installation-related issues». For Morgan Tecnica, it is essential to carefully manage interventions that can be carried out over the phone. «We have structured ourselves to ensure high-level telephone assistance, with immediate response, to solve any query that comes from every part of the world». The customer now has the certainty of being assisted in the best possible way and in the shortest possible time.
THE INTRODUCTION OF LEAN PRODUCTION
Even before addressing the Service and the post-sales approach, Donini considered it essential to renew the entire logistics-production aspect. «Change, first and foremost, must be cultural. What I have learned from my work experiences is that Corporate Culture is not just an element of the game: it is the game itself. To be successful, there must be the collective will of the organization, and above all, within that organization, there must be the same values, which will guide the change».
The Lean philosophy has been implemented with the aim of reducing the Lead Time of orders and providing the highest quality service possible. «The markets are becoming increasingly competitive: those who order a machine need to receive it quickly. For this reason, Morgan Tecnica has also set up predictive work, through a system that predicts the extent of sales, in order to be faster in delivery. This is a celerity that is difficult to achieve in an industry with a high incidence of customised installations».
The 2023 innovation, which brought the new Director of Operations, is the creation of two dedicated product lines – one for cutting machines and the other for laying machines – capable of guaranteeing precise Lead Time and a rhythm, called Takt Time, in line with market objectives. Takt Time requires synchronized assembly stations, for a continuous and balanced production flow.
THE KEY ROLE OF LOGISTICS
Even more important than production is the logistics in the broad sense, which must be adequate and follow the right production pace. «In 2024, we will focus on the entire Supply Chain, with the aim of cooperating with suppliers who deliver punctually, when the process requires it, surpassing the concept of “buy and stock”. For this, specific audits need to be conducted to assess if a supplier is qualified in this regard».
The concept is to move warehouses closer to suppliers, thus ensuring that materials are stored directly by third parties to avoid storage within Morgan Tecnica.
«To set up this model, the necessary path is a Supply Chain 4.0, therefore a portal with suppliers that becomes a communication channel through which everything can be managed: order, order confirmation, delivery, and delivery postponement».
Morgan Tecnica also intends to reduce the management complexity of purchasing materials needed for production, thanks to a path of industrialization and standardization of the product. This involves a process of rationalizing the supply chain, with an outlook of increasingly closer collaboration with suppliers, who are increasingly becoming true working partners.