Rex. Sustainable, compact, and China-free
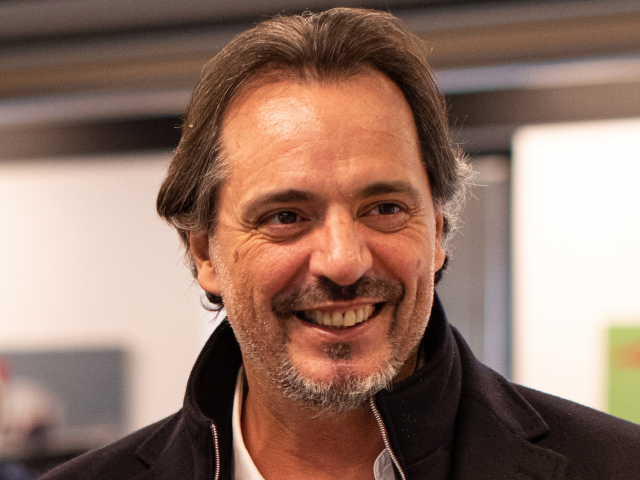
Fabrizio Giachetti / CEO
In a perspective of constant innovation and continuous improvement, Morgan Tecnica launches new products or versions with an average of three years. «In the development of the new REX cutting machine, our R&D department has adeptly identified the necessary features for the success of the new automatic cutting in the market. The challenges from 2020 onwards have prompted us to make decisions that have proven successful from a marketing standpoint».
THE DEVELOPMENT PATH
«The initial goal was to improve the performance of our Next 2 Delta cutting machine while simultaneously adopting components that would make us resilient to geopolitical events, ensuring security both in the present and in the future». Sourcing electronic components in the recent past has indeed been challenging. «We have all become aware of how dependent we are on China and the resulting slowdowns: regardless of the product’s quality, if the components are missing, production is compromised. We needed a change in strategy, with different suppliers».
There was another significant factor: «For a certain period, maritime costs increased tenfold, while air costs increased more moderately. So, we designed a machine that could be transported by air, more compact and divisible into two easily assembled blocks without compromising performance and quality».
Finally, there’s a greater sustainability aspect. «We committed ourselves to creating a high-performing, sustainable solution with lower consumption, in line with the Green Deal directives». REX has two sustainable patents for considerable energy savings, with a 50% reduction in consumption compared to traditional cutting machines in the same range.
INNOVATION MADE IN EUROPE
In the REX, Chinese components make up less than 1%, while 70% is Made In Europe. This is especially true for electronics, which protects against tariff uncertainties or geopolitical situations that complicate their availability. «In addition to ensuring our security, this decision has been attractive from a marketing standpoint. We have formed a partnership with Bosch Rexroth, a German company that has invested in achieving independence in semiconductors in recent years. All components we purchase are 100% Made in Europe: this attests to our commitment to reliability and ensures uncompromising quality».
COMPACTNESS AND MODULARITY
Thanks to its reduced size and the ability to be divided into two parts, REX can be transported by air. «This allows our customers to choose the shipping option that best suits their needs, and we can offer fast delivery at an affordable price».
The total length is about one meter shorter than previous models. The machine can be shipped without disassembling the technological part, such as the cutting area, the main axes of the machine, and the cutting head. «Furthermore, thanks to a new fan inside the machine, we have been able to reduce the size of the suction tank: this has improved suction efficiency and allowed us to install a power of approximately 40% lower».
THE TWO SUSTAINABLE PATENTS
To ensure sustainability performance with the lowest possible energy consumption, Morgan Tecnica has filed patent applications for three patents, two of which focus on sustainability.
The first, ERS (Energy Recovery System), eliminates energy waste and recovers energy similar to what happens during the braking process of hybrid cars. Whenever the motors decelerate, the dispersed energy is recovered and put back into circulation, «thanks also to the “Smart Energy Mode” functionality of Bosch Rexroth. This dampens peak consumption and gives the machine strong energy efficiency».
The second patent arises from the fact that all cutting machines use large aspirators, responsible for most of the energy consumption, to immobilize the fabric during the cutting operation, creating an airflow that is expelled upward through the exhaust chimney. Morgan Tecnica has therefore invented a small wind turbine, Spin Power, which harnesses that airflow to generate electricity.
«We had estimated that ERS and Spin Power would result in a 40% energy saving, but the forecast has proven to be conservative: the savings in some cases exceed 50%». All this translates into lower bills and significant tax breaks thanks to the benefits associated with Industry 5.0, as envisaged by the National Recovery and Resilience Plan (PNRR) that will soon come into force – it is thought – also retroactively.
THE THIRD PATENT
Automatic cutting systems are designed to process a large number of shapes, and among these, some may require special precautions. Since there is currently no algorithm that can pre-emptively and definitively recognize a problematic shape, operators tend to reduce the overall cutting speed, and consequently, productivity suffers.
«We have developed a collaborative approach that combines operator experience and automatic procedures. When the operator encounters a problematic shape, they simply input it into the Morgan ADB (Active Database) with a single click, and corrective attributes are applied. The user can decide whether to create a personal local database or share it via Morgan Tecnica – which securely filters shapes and attributes – with other ADB users who have registered for a specific subscription».